Case Study
Beef Block
Trim System
Birchwood Foods
The challenge.
Birchwood Foods needed to quickly separate tempered beef trim blocks back into their originial pieces for treatment with an antimicrobial spray. One of their larger fast food clients required the treatment on all beef for their burgers.
The solution needed to be an integrated system to take beef trim blocks from their microwaves, break them apart without cutting or grinding, spray the pieces down, and take to further processing.
Their current system required 22 employees over two shifts moving product from one part of the facility to another — not a very efficient or cost effective method to compete with other processors.
Requirements
- Separate beef trim blocks
- No cutting or grinding (per USDA)
- Automatically feed from microwaves
- Reduce labor & processing time
- Increase safety
Key solutions.
Our solution was to design, fabricate, and install a complete system to move beef trim blocks from the microwaves into a custom piece of equipment designed for Birchwood Foods.
- Custom equipment design & fabrication
- Processing line layout
- Conveyor design & fabrication
- Platforms & ergonomic stands
- Control system
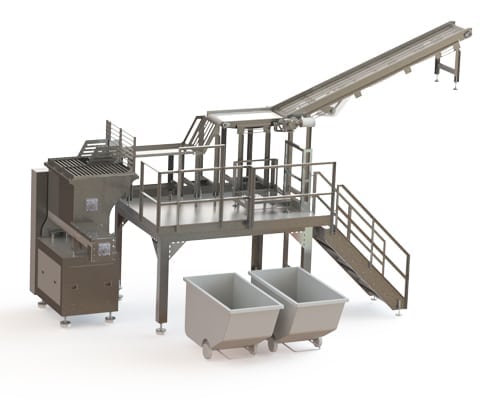
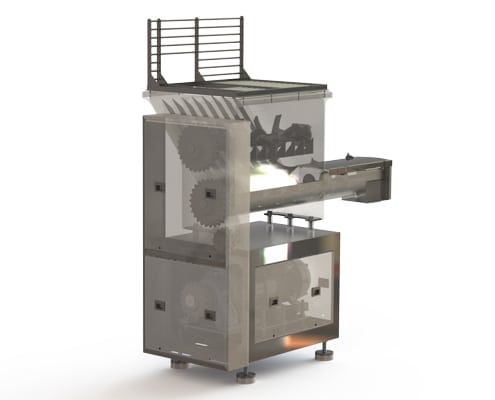
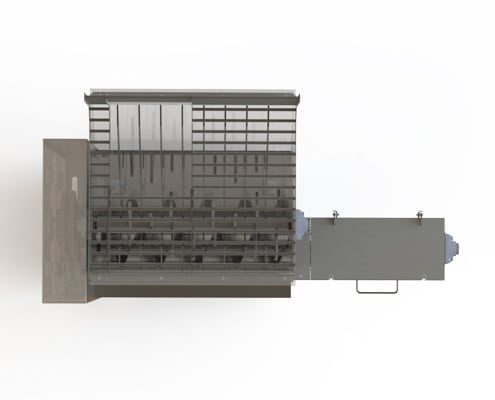
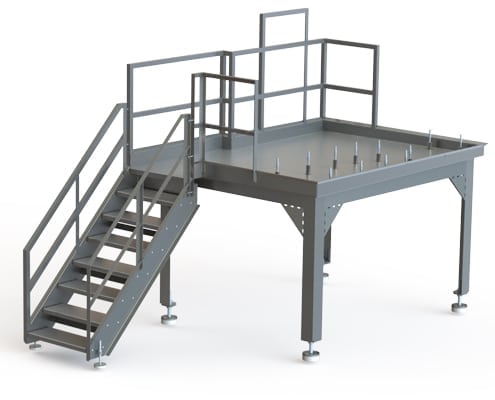
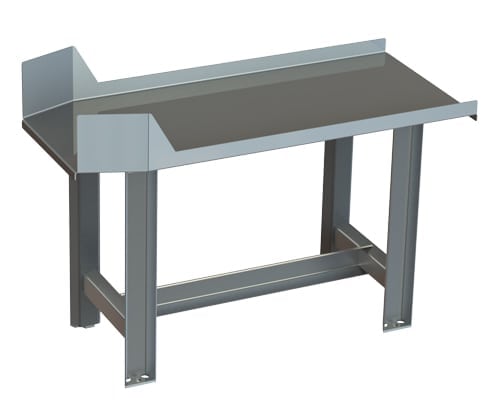
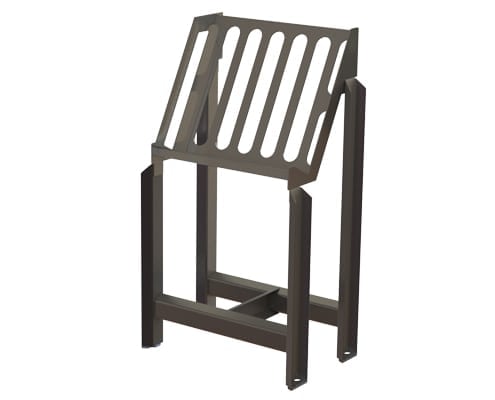
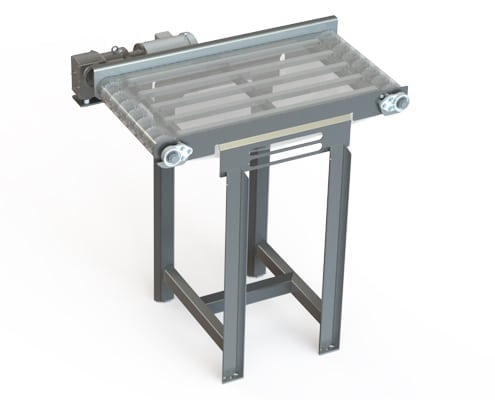
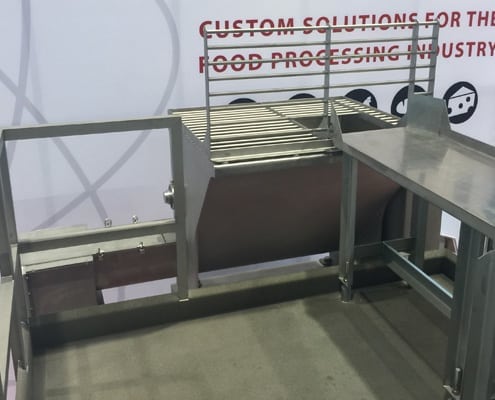
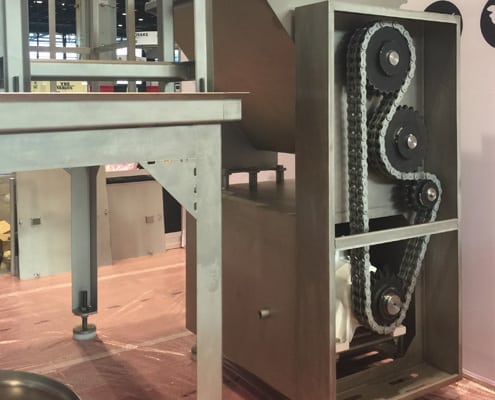
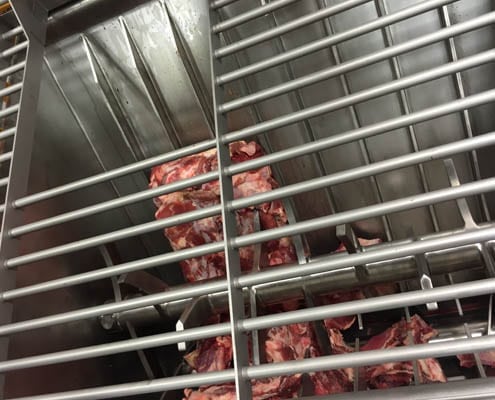
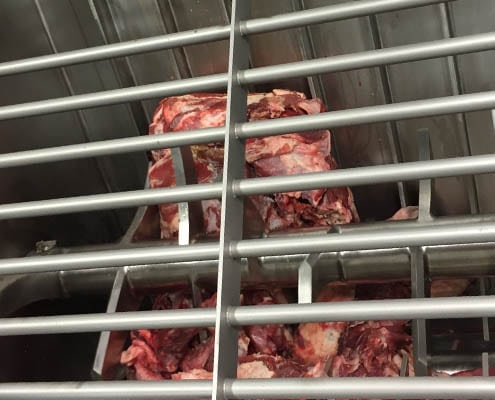
The results.
The results speak for themselves. The system we designed decreased labor from 22 employees working over 2 shifts down to 7 employees working 1 shift while producing the same amount.
What the customer said.
Fusion Tech worked with us to take our current operation of processing frozen beef trim blocks that took 2 shifts and 22 employees to reach our product goals and reduced it to a 1 shift operation manned by 7 people. They designed a new piece of equipment for us that took our semi-frozen trim blocks and gently broke them up so we could treat each piece to eliminate any bacteria. We told them what we needed the system to do, and they went to work researching options and designing a system that met our needs and saved us time and money. We are able to process the same amount of product in 1 shift that we did in two. I would highly recommend working with the team at Fusion Tech.
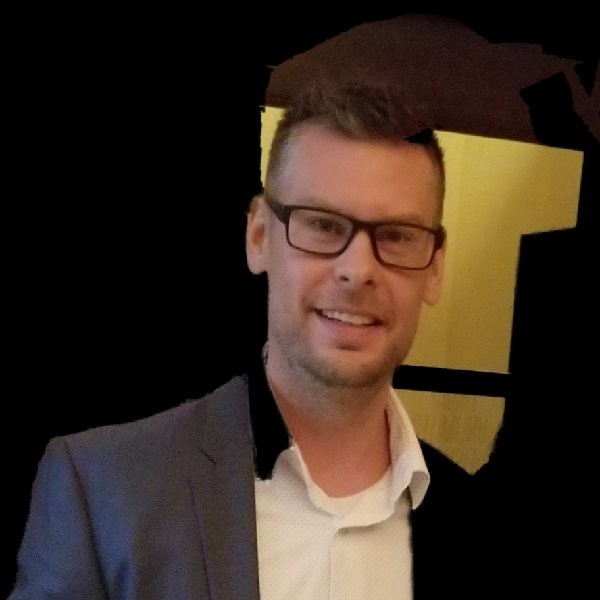