Case Study
Tipper-Tie
System
Genesys Systems Integrator
The challenge.
Genesys Systems Integrator, a business, technology, and process integrator, came to us needing a new process to move product in between existing Tipper Tie, slicing, and packaging stations.
The system needed to integrate into the Tipper Tie controls to keep the OEM’s machines full while in operation, which required photo-eye integration, controls and automation, and accumulation conveyors.
Upon meeting with the client and visiting the plant, the Fusion Tech team designed and fabricated a complete, automated system to keep product flow in line with production goals.
Requirements
- Model all equipment
- Integration with existing equipment
- Integration into Tipper Tie controls to keep Tipper Ties full
- Angled conveyors
- Ham loading chutes
- Crossovers
- Accumulation conveyors
- Photo-eye integration
- Controls and automation
Key solutions.
- Controls & Automation
- Custom Equipment Design
- Integration with Existing Equipment
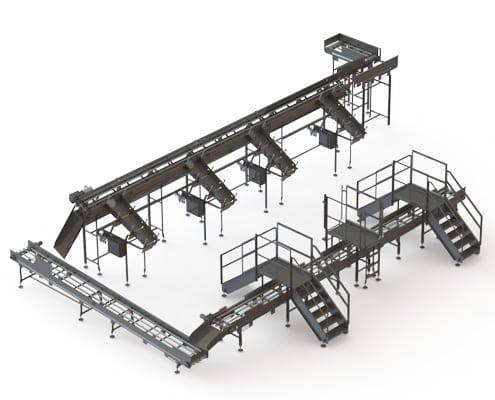

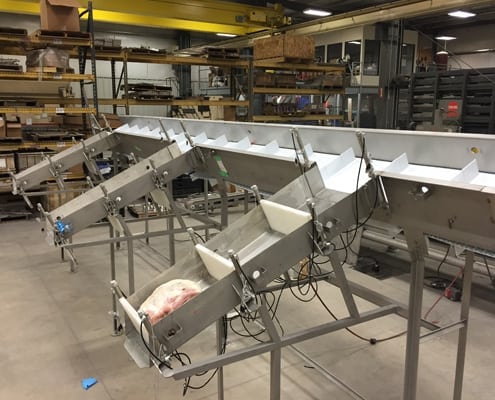
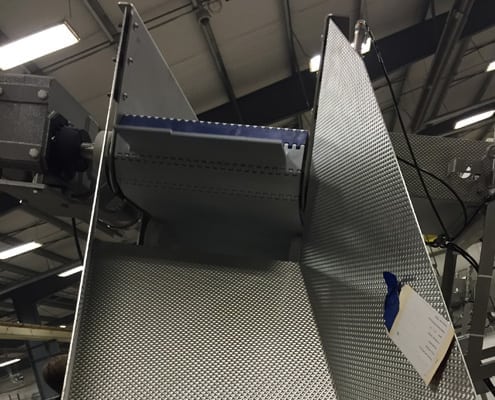
The results.
Genesys Systems’ client experienced an increase in product yields and a consistent flow of product into their Tipper-Tie machines, reducing down time and operating expenses.
- Increased Product Yields
- Decreased Processing Time
- Decreased Operating Expenses